Ulinastatin is a valuable therapeutic protein used in the
treatment of various inflammatory and immune-related conditions. As the demand
for this medication continues to rise, ensuring its manufacturing process is of
utmost importance to maintain its quality and efficacy. In this article, we will
explore the key aspects of Ulinastatin manufacture and the measures taken to
ensure its production meets the highest standards.
Quality Control: Manufacturers of Ulinastatin adhere to stringent quality
control measures throughout the production process. This involves rigorous
testing of raw materials, monitoring of manufacturing parameters, and conducting
comprehensive analysis of the final product. Quality control protocols are
implemented to verify the identity, purity, potency, and safety of
Ulinastatin.
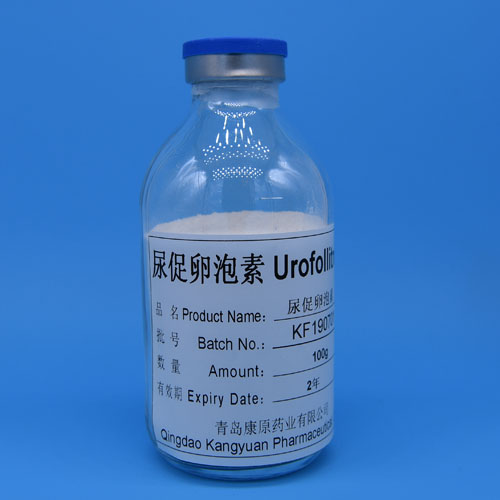
Good Manufacturing Practices (GMP): Ulinastatin manufacturing strictly
follows Good Manufacturing Practices, a set of guidelines and regulations that
ensure the consistency, safety, and quality of pharmaceutical products. GMP
covers various aspects such as facility design, equipment calibration, personnel
training, documentation, and record keeping. By adhering to GMP standards,
manufacturers ensure that Ulinastatin is produced in a controlled and sterile
environment.
Validation and Process Optimization: Manufacturing Ulinastatin involves
complex biochemical processes. Before full-scale production, manufacturers
conduct extensive validation studies to optimize the manufacturing process and
ensure reproducibility. This includes validating critical parameters, such as
fermentation conditions, purification techniques, and formulation stability.
Through meticulous optimization, manufacturers can achieve consistent and
reliable production of Ulinastatin.
Regulatory Compliance: Ulinastatin manufacturing is subject to strict
regulatory oversight to guarantee its safety and efficacy. Regulatory
authorities, such as the Food and Drug Administration (FDA), conduct inspections
and audits to ensure manufacturers comply with the necessary regulations.
Compliance with regulatory requirements is crucial in maintaining the quality
and reliability of Ulinastatin.
Continuous Improvement: Manufacturers are committed to continuous
improvement in Ulinastatin manufacturing. This involves ongoing research and
development to enhance production techniques, optimize yield, and improve
product stability. By staying updated with the latest scientific advancements,
manufacturers strive to deliver Ulinastatin of the highest quality to healthcare
providers and patients.
Conclusion: The manufacturing of Ulinastatin is a complex process that
requires strict adherence to quality control, good manufacturing practices, and
regulatory standards. Through meticulous validation, optimization, and
continuous improvement, manufacturers ensure the production of Ulinastatin that
meets the highest quality and efficacy standards. By upholding these standards,
Ulinastatin continues to be a valuable therapeutic option for patients in need
of anti-inflammatory and immune-modulating treatment.
Note: The above article is for informational purposes only and should not
be considered as medical advice. Please consult a healthcare professional for
any medical concerns or questions regarding Ulinastatin or its manufacturing
process.